Agristrand Mankato, LLC plans to manufacture soybean-straw door cores and furniture panels — a renewable alternative to wood particleboard. The $10.25 million start-up has purchased the former Environ Biocomposites factory in Mankato and is set to begin production this spring.
Agristrand Soy Board is a rare value-added use for soybean straw, says Agristrand board member Dan Beenken, a farmer from Buffalo Center, Iowa. “Most new uses for soybeans have been for meal and oil. There’s been very little done with soybean fiber.”
The idea for soybean particleboard was born over a cup of coffee.
Tom Neel, president of Neel Lumber Company, Panora, Iowa, was talking with three friends over coffee about the high price of particleboard, which is widely used in doors, furniture, cabinets and counters. Particleboard is a composite of wood fragments and resin, bonded together under heat and pressure. Prices for the material fluctuate sharply, depending on wood supplies and value.
Neel wondered if there wasn’t a more price-stable source of cellulosic fiber that would work as well as wood. That question led the four Iowa businessmen — Neel and Agristrand co-founders Tim McDermott, Barry Monaghan and William Priestley — to the woody stems of soybean plants.
Twiggy stems
Soybean stems, which look like dried twigs, have several advantages for particleboard, says Dan Biller, Agristrand vice president of sales and marketing. “They have characteristics similar to wood,” and the soy-straw board is comparable to wood-based products in look, feel and uses, Biller says. The stems are also abundant and easy to collect.
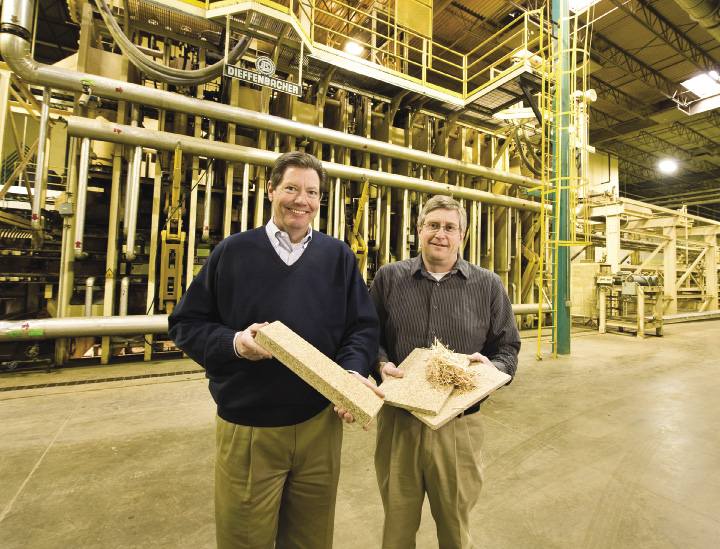
The Agristrand founders worked with the USDA Forest Products Laboratory in Madison, Wisc., to formulate a soy-straw particleboard that meets industry requirements for composite building material. “We achieved those standards in 2010,” Biller says.
AURI helped the company test ways to chop and clean the straw before it’s pressed into boards. Work at AURI’s coproducts pilot lab in Waseca led to a proprietary method for preparing the raw material.
“AURI has been very helpful with the up-front processing,” Biller says. “Our conditioning equipment is portable, so it can be taken out to the straw storage sites.” That cuts the cost of trucking bulky round bales to the factory. The conditioned soybean straw looks and handles like
wood chips.
At the factory, soy straw is combined with “eco-friendly” resins that don’t add formaldehyde — a strong selling point for the green building materials market, Biller says.
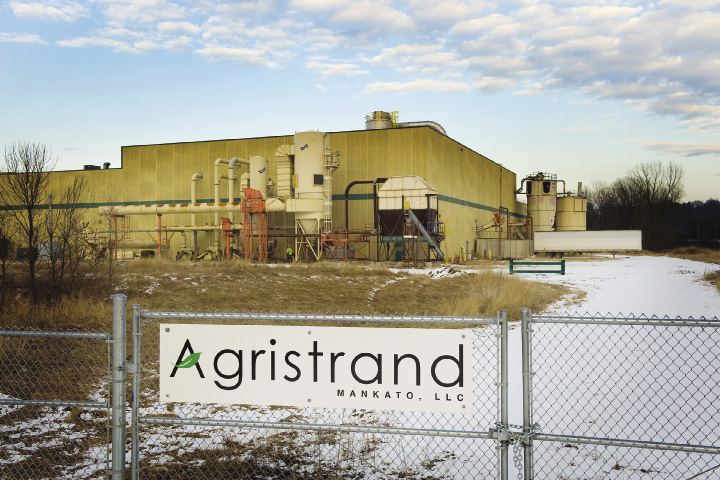
Another advantage: “Our process captures all the dust and uses no water.” Those are two common environmental issues with ag fiber processing, he says. AURI is helping the company pelletize the captured dust and fines generated during manufacturing. Potential uses for these byproducts include biomass fuel pellets and animal bedding, says Al Doering, director of AURI’s coproducts lab in Waseca.
Late last fall, Agristrand completed a $10.25 million capital drive and purchased a 160,000-square-foot factory in Mankato. The facility, constructed in 1998 for about $50 million, has an annual processing capacity of 40 million square feet of board. It had been idle for 15 months.
Agristrand will finish upgrades to the plant this spring. At full production, the factory will employ about 50 workers and process soybean straw from 45,000 acres in southern Minnesota and northern Iowa.
Making buildings greener
The U.S. furniture and building trades used more than 2 billion square feet of particleboard in 2011. In such a huge market, “we don’t need to be a big player to do well,” says Biller, who has spent his entire career selling
building materials.
He’s positioning Agristrand soy board as a niche product that offers a “unique green value.” Soy-fiber door cores and panels should qualify for USDA’s BioPreferred Program, which promotes renewable products. The soy-straw panels also contribute points towards the U.S. Green Building Council’s LEED certification. A growing number of builders and institutions are pursuing this badge of environmental sustainability, Biller says, “and more consumers are asking for it, too.”
Agristrand’s Minnesota location is also a marketing plus, Biller says. Most particleboard manufacturers are located on the Coasts. But “there are a lot of door manufacturers here in the Upper Midwest.” For those markets, Agristrand has a significant shipping advantage over more distant suppliers, he says.
Agristrand’s strong management team is another advantage, Doering says. The company’s executives “have a minimum of 25 years of experience each in the wood products industry or the financial industry.”
That struck investor Dan Beenken. “I’m very impressed with their passion for what they’re doing, their management capabilities. Their skills complement each other very well, and the same is true of the board members.”
Launching this new business has been a tough yet rewarding challenge, Biller says. “Building a company, putting people back to work, making a useful product. We’re very proud of that.”
AURI & Agristrand
Idea to Opportunity: Agristrand wanted to make particpleboard out of soybean fiber.
Outcome: AURI helped the company develop a proprietary process to chop and clean the raw material before it’s made into panels. The company will begin manufacturing operations in Mankato this spring.
Area farmers supplying soy board raw material
Many of Agristrand’s 45 shareholders are farmers from Minnesota and Iowa, who will also supply the raw material to make soy-straw particleboard.
“We are excited about our partnership with local farmers,” says Tom Neel, Agristrand president and CEO.
Tom Strueker, who farms in Emmet County, Iowa, invested in the start-up and serves on the board. He was attracted by Agristrand’s “good product and good management team.”
Last fall, Strueker supplied 700 acres of soybean straw. He disconnected the chopper on his combine, saving about 10 percent on fuel consumption, and deposited the residue in windrows. A contractor baled the straw and transported it to a northern Iowa storage site. “All we take is the stem,” Strueker says. “We pick it up loosely so the leaves and pods stay on the field.”
Straw yield in 2011 averaged about one ton per acre, he says. Soybean stems supply very little organic matter or nutrients to the soil, he says, so removing them isn’t a concern.
“We’re actually fighting too much residue at times,” says Dan Beenken, a farmer from Buffalo Center, Iowa. Like many Iowa and Minnesota growers, he has added more years of corn to his crop rotation. “So soybean residue removal isn’t really an issue. And we’re only taking about a ton per acre once every three years or so.” He harvested 210 round bales of soy straw from a 130-acre field last fall. Afterwards, “the field didn’t look much different than normal.”
Agristrand pays $45 per ton for soy straw, baled and delivered, for a net farm return of about $15 per acre, Beenken and Streuker estimate.